トップページ > 溶接におけるVA/VE提案
溶接におけるVA/VE提案
①大型製缶部品の溶接接合部の設計ポイント1
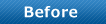


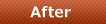

製缶品の溶接において、上図のように溶接ラインを合わせてしまうと応力が集中し、強度面で非常に弱くなってしまいますが、溶接ラインをずらし応力集中を避けることで強度を保つことができます。
②大型製缶部品の溶接接合部の設計ポイント2
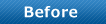


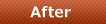

製缶品の溶接において、上図のように溶接ラインを合わせてしまうと応力が集中し、強度面で非常に弱くなってしまいますが、溶接ラインをずらし応力集中を避けることで強度を保つことができます。
③鋼管や形鋼の組み合わせ時における溶接工数削減のポイント1
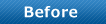


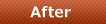

同サイズの角型鋼管とH型鋼を溶接するような場合、角のR部分に隙間ができ、溶接の工数が増えてしまいます。そこで異なるサイズの部材をうまく用いれば、隙間を無くすことができ、工数削減になり、コストダウンにつなげることができます。
④鋼管や形鋼の組み合わせ時における溶接工数削減のポイント2
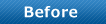


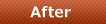

鋼板を組み立てて部品を作るようなケースでは溶接量が多くなり、結果コスト高になることが多く、鋼板の組立ではなく規格品の形鋼を利用するとコストダウンにつながります。
⑤形鋼の使用方向の変更による溶接工数削減のポイント
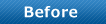


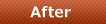

チャンネルやH鋼の内側は溶接機の制限から入り口のみしか溶接できないため、強度不足になる上に開先溶接が必要なので工数がかさむが、部材の方向を変更することで下図のように溶接が容易になります。
⑥部品設計時における溶接記号表記の明確化によるコストダウン1
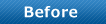


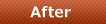

脚長が明確でない場合の溶接は薄肉側の100パーセントと慣例化されているが、溶接時間が長くかかってしまいます。強度を必要とする場合以外はすみ肉溶接を薄くすることで工数削減を行うことができます。
⑦部品設計時における溶接記号表記の明確化によるコストダウン2
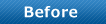


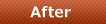

両面溶接が図面上で指示されていても強度を必要とせず形状保持が目的の箇所であれば、片側溶接に指示を変えることで工数を削減することができます。
⑧部品設計時における用途に合わせた溶接方法の選定ポイント
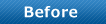


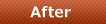

上図のように未溶接部が存在する場合、溶接部が少ないので加工コストは下がるが錆などが発生し易く、長期的に見ると環境によってはコストアップにつながります。そのような場合は全体に溶接を施すことでコストダウンにつながります。
⑨大型製缶部品の溶接部におけるコストダウン設計のポイント1
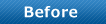


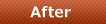

上図のように溶接する箇所の大きさが同じ場合は開先溶接等が必要となり、加工コストが高くなってしまいます。このようなケースでは上板と本体板のサイズを変えることにより、通常の溶接を行うことができます。
⑩大型製缶部品の溶接部におけるコストダウン設計のポイント2
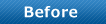


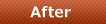

上図のような図面では溶接部に開先溶接を施す必要があり、加工コストが高くなるが、溶接しろを設けることでコストダウンにつながります。
⑪大型製缶部品の溶接部におけるコストダウン設計のポイント3
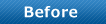


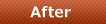

上図のように部材の端部に揃う位置にリブを置くと、内側はすみ肉溶接できるが、外側は開先溶接と仕上げ面の加工のためグラインダー仕上げが必要ですが、リブの位置を変更することでグラインダー仕上げを不要とすることができます。
⑫大型製缶部品の締結部の設計形状変更によるコストダウン1
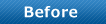


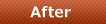

タップ加工を板に施しているような上図のケースでは、タップ加工の変わりに板にナットを溶接することで、工数を削減することができます。
⑬大型製缶部品の締結部の設計形状変更によるコストダウン2
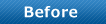


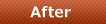

部品と部品の締結を片側にタップ加工を施した上でボルト止めしているような場合、ボルトとナットによる締結に変更し両側から挟むような形にすることで工数を減らし、コストダウンにつなげることができます。
⑭大型製缶部品のリブ形状設計のポイント
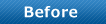


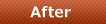

上図のようなリブ形状にしてしまうとリブを斜めに切断することになりブラケットの直角度を出すことが難しいが、下のように切断すれば直角度を容易に出すことができます。
⑮形鋼の使用方向における溶接工数削減のポイント
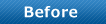


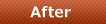

2つの同サイズの部材を組み合わせる場合は組み合わせの向きにより、片方の部材を切り欠けに加工した上で溶接が必要となり、コストアップになります。
⑯製缶架台設計時の精度・強度アップのポイント
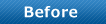


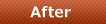

4本足の架台は強度・精度を出すことが難しいため、梁やリブを入れることで強度を向上させることができます。