トップページ > 穴あけ、タップ加工におけるVA/VE提案
穴あけ、タップ加工におけるVA/VE提案
①部品設計時におけるタップサイズ統一によるコストダウン
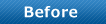
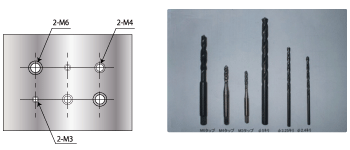

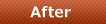
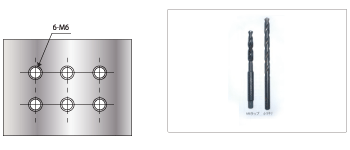
ひとつの部品に異なるサイズ径の穴が存在すると工具取替えの時間が生じ、工数が増大します。設計段階から穴径サイズを統一することができる場合は、加工工数を減らしコストダウンにつなげることができます。
②部品設計時におけるタップ穴サイズ変更によるコストダウン
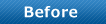
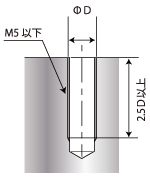

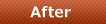
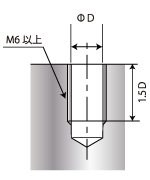
小径タップでタップ加工を行う場合、穴が深いと折損リスクが高くなります。このような場合、穴径が大きくても問題なければ、径と穴の深さの比に注意して設計することで、折損リスクを減らしコストダウンにつなげることができます。
③部品設計時におけるタップ穴加工コストダウンのポイント
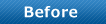
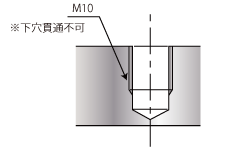

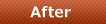
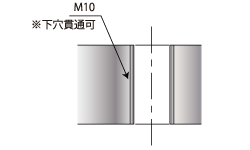
2つの同サイズの部材を組み合わせる場合は組み合わせの向きにより、片方の部材を切り欠けに加工した上で溶接が必要となり、コストアップになります。
④設計時における穴開け加工の共通化によるコストダウン
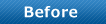
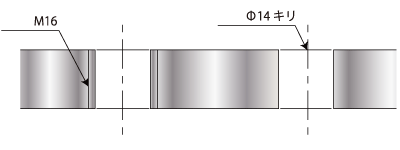
上図のような4本足の架台は強度、精度を出すのが困難です。

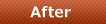
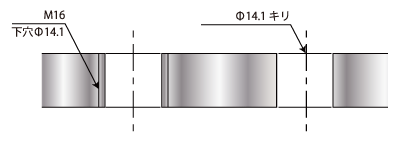
リブや下部に梁を入れることで強度・精度を出すことができます。
タップ加工と精度を要求されないキリ穴が両方存在するようなケースでは、タップ穴の下穴加工に用いる穴径とキリ穴径を統一することで工数を削減でき、コストダウンにつなげることができます。
⑤厚い窓抜き加工における部品設計のポイント
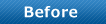
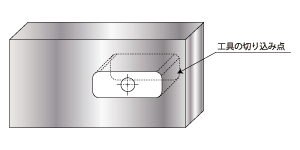

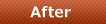
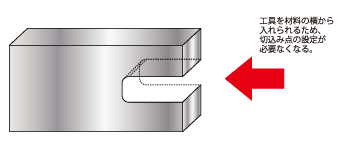
上図のような窓抜き加工は切り込み点の設定と穴加工が存在するため工数が多くなりますが、設計上問題ない場合は、下図のように設計変更することで加工工数を減らすことが可能です。